6 common garment quality production issues that you can avoid
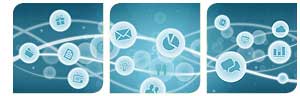
Putting a piece of garment together is a form of art and we all know how to appreciate the beauty of a flawless one. It is, however, a different story to put 5000 or 500,000 pieces of garment together by different workers and this is where many garment quality issues arise in production lines, possibly causing delays in shipment, additional repair costs, non-compliance risks and other impacts to your fashion businesses.
We have spoken to our technical teams with decades of experience in fixing issues during garment production and consolidated several common quality issues that could happen to your apparel, with tips on how to avoid them.
Sizing matters
One very common issue with garments is incorrect sizing as a result of poor stitching and sewing. In many cases, the difference between each size could be rather small and potentially the workers are not aware of which sizes they are working on, hence sewing the garment too tight and causing wrong sizing. This could also be a result of poor storage and sorting of fabric after cutting, causing different fabric sizes to become mixed and thus sewn incorrectly.
This can be improved by ensuring proper fabric storage management and switching the sizes of the fabric being worked on for one size up – say for example, after working on the M batch, arrange the same lines to work on XL so the variance is more significant to the workers, reducing the chance of incorrect sewing.
Fabric utilisation
How much a fabric shrinks is closely related to the garment quality. To save costs, manufacturers utilise every inch of the fabric when placing the markers, without taking the shrinkage performance of the fabric into consideration.
While the garment would hold in good shape during the assembly process, deforming in garment construction occurs later during the wet processing phase or home laundry after being purchased by the end consumers.
A pre-production meeting should be held and a review of shrinkage performance from fabric test reports can best determine the cutting pattern.
Workmanship defects
Needless to say, workmanship is crucial in determining quality during garment manufacturing. For a well-managed factory, skill set training should be offered to workers with training records documented. This is especially the case if special sewing techniques or expectations are required which require relevant training.
These records can be checked anytime by you or your QA/QC team if you visit the factories. Onsite random checks of workmanship are a great way to examine proficiency levels.
Chaotic goods storage
Producing non-compliant garment goods is inevitable but preventing non-compliant goods from entering your shipment can be achieved by a well-defined management system.
Clear and separated zones/areas should be laid out to store goods according to their statuses – Green for compliant goods, yellow for non-compliant goods (pending examination by line heads to see if repair is possible), and red for failed goods.
In order to confirm these detailed arrangements, you can assess the factories in person.
Sharp object risks
While it seems humorous to tell you that your colleagues at warehouses or shops could find scissors fallen from a factory packing area in cartons or worse, broken needles left in the garment from the sewing process, the reality is the situation is serious as it poses risks to workplace and/or consumers safety.
Similarly, management systems should be in place at factories to control the placement and replacement of sharp objects like scissors, cutters, needles and thread trimmers. Spot checks of a factory’s metal detection process and sharp object control policy during different stages of inspection can be arranged. A final random inspection that includes metal detection helps in this aspect as well.
Safety standards concerns
Recalls of childrenswear are seen from time to time because of safety non-compliance. Reviewing, for example, the length of drawstrings of your child jackets or pull strength of beading for infant tops at production lines, is a highly effective preventive measure that can be done by your QA/QC team on-site. Critical failure like this can be monitored more closely, elevating your quality control plan.
If you are working with a trusted supplier, they can implement all these preventive suggestions into their production lines, giving you an extra level of assurance in terms of your garment goods’ quality. If you are coming across new suppliers, or the suppliers lack the resources and knowledge to deliver what is required, your in-house QA/QC team can provide support to ensure goods’ quality level.
Alternatively, we offer a comprehensive QA-QC Programme for the Apparel and Garment Industry that you can leverage almost instantly to cost-effectively improve quality issues for your garment production.
Learn more about the programme and do not hesitate to reach out for customisation anytime!