Explaining technical audits for the garment industry – definition, assessment criteria, and checklist highlights
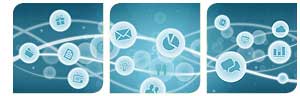
After spending hours searching, on the phone to your new garment suppliers, and reviewing their catalogues, sample photos, certificates and past purchasing orders, what next? Are you ready to place an order? Without a technical audit to really understand the competency of your potential new partner, it is probably too early to do so – otherwise, you might run into problems with production quality, which could lead to financial loss.
What is a technical audit?
A technical audit is a detailed evaluation of your new supplier’s capabilities and capacities. It gives you extensive visibility of how well the factory will be able to meet your requirements in terms of production and quality, and reveals how proactively the factory manages these aspects. Findings from the audit will help you to make an informed decision about whether to place an order, and to understand the level of risk associated with this production.
In many cases, technical audits are also carried out at the sites of existing suppliers on a 12-month basis, in order to maintain a good understanding of their performance, so as to identify possible areas of improvement and ensure consistent production quality.
What are the assessment criteria for a technical audit for the garment industry?
A major consideration in a technical audit assessment is the Quality Management System. Other common criteria include:
- Quality Management System
- Factory Environment
- Product Control
- Process Control
While it may initially seem easy to meet just four criteria, the full assessment checklist can be very extensive, in actuality. Using the Eurofins’ technical audit protocol as an example, this checklist comprises more than 250 items and has been tailored to ensure every detail of garment production is inspected through a multi-pronged approach.
Common checklist of garment technical audits
To help you with designing your own checklist for garment suppliers, we have shared some key points below – but, of course, your complete list will be much longer.
Quality Management Systems
- A quality assurance manual, outlining the quality procedures, exists and is clearly communicated to workers.
- There are clear quality goals indicating the target pass rate.
- The quality control (QC) team are independent from the production unit.
- There are clear duties, responsibilities and accountabilities among the product safety team, regulatory compliance team, and quality team.
- The complaint log exists and is well-established, as well as an investigation record.
- Staff from different teams are provided with relevant knowledge training and the training records are documented.
Factory Environment
- A proper working environment, which covers factors like temperature, humidity and hygiene, is critical to avoid contamination of raw materials, especially for leather and metal components, as well as sufficient lighting for quality inspection.
- Proper metal policy, which includes the review of the written metal policy, proper securement of sharp tools at workstations, a written needle policy, and a proper needle log.
- Proper waste and waste disposal control, which covers the review of proper waste storage and segregation areas, and valid permits for in-house and external wastewater treatment systems.
Product Control
- Product development team should be familiar with garment legislation and standards. If you carry childrenswear, which is subject to more stringent requirements, you will want to be more specific on this check point, so that products can be right from the design stage.
- Proper control during design, risk assessments and the validation of product compliance, since these are fundamental to the garment’s quality.
- Proper procedure to handle non-compliant products, from quality control methods to non-conforming documentation, disposal of defect goods, and notification to clients.
Process Control
- Out-sourcing is done in a compliant way; out-sourcing is a common practice in the garment industry, but unknown out-sourcing could pose high risks to product quality and the integrity of your supply chain.
- Proper storage of raw materials like fabrics and yarns by batch/shade to avoid incorrect usage.
- Proper verification of the colours of important components/materials with light boxes.
- Proper monitoring of the physical and chemical compliance of incoming materials’ test results.
- Proper completion of a pilot run prior to full production, in order to identify and minimise potential quality issues.
- Proper quality control (QC) plan, which oversees 100% workmanship and visual defect inspection at the end of knitting/sewing lines, and validation of critical measurement pre and post washing and pre/final inspection.
- Proper machinery is used during production, such as using fusing machines for fusing, and appropriate/designated machines for attaching accessories.
- All production should pass through the metal detection process.
It is similarly important that you weigh each checklist item appropriately. Forming a matrix which indicates both the tolerance and compliance level, and applying this to checklist items, depending on their risk levels, is a practical way to handle scoring and assessment.
When executed properly, a technical audit can generate useful insights into your working partners’ conditions, which allows both parties to make well-informed decisions. During the audit and follow-up processes, the parties can cultivate a deeper understanding and build a stronger relationship as well.
If you need any assistance in setting up your programme, don’t hesitate to contact us for a discussion anytime.