[Expert View] What Will the Post-Coronavirus Supply Chain Look Like?
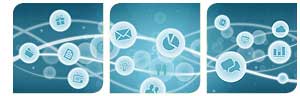
Original article appeared in Sourcing Journal on 1st April 2020
The impacts of the COVID-19 pandemic will dramatically change many aspects of life and the way we do business.
Several weeks ago, I was asked to participate in a webinar panel on the impacts of the coronavirus on supply chains. At the time, the focus of the discussion was on the impacts on supply resulting from the spread of the virus in China. The extension of the Lunar New Year factory closures was impacting production of orders in China and the provision of key materials to other countries in the region. In a matter of just a couple of weeks, the focus of that discussion went from consideration of the virus’ impact on supply to the impact on demand and resultant supply-chain implications.
Clearly, the initial China experience with the virus provided some important lessons in supply-chain management—challenging truths and highlighting issues with the just-in-time systems that have come to be the norm. From the outset, key lessons related to knowing the supply chain were at the forefront—not just the final link but key sources of supply related to materials, having contingency plans for interruption of supply, and understanding the capabilities and vulnerabilities of critical elements within the value chain.
Moving forward, there will be many more lessons and experiences. As a long-time practitioner in the field of supply chain quality and risk management—with a particular focus in the area of social responsibility and supply-chain working conditions—I have a particular concern related to experiences from previous cataclysmic events that could serve to inform current activities.
There should be no question that the events associated with the global pandemic will have devastating financial implications for entities around the world, with the apparel value chain being one of the most dramatically impacted. From retail employees through the more than 40 million workers in factories producing the goods for brands and retailers, the tight-margin, just-in-time world presents significant risks and challenges.
To be clear, there will be business failures and closures that will negatively impact individuals at all levels and leave those at the lowest levels of the value chain most at risk, due to the financial structures of developing-world factories and the limited or non-existent social safety nets in those environments. There has been a fair amount written about these challenges and in this regard I do not have anything to add.
The supply-chain management responses specifically with respect to working conditions for two significant events of this century—the events around 9/11 and subsequent economic downturn and the Great Recession of 2008/9—should be considered as we move on from the effects of the pandemic.
In 2001 and again in 2008, companies adjusted their efforts and engagement on supply-chain working conditions. Fundamentally, this makes sense as there is a need to manage resources and make choices. In 2001, there was far less global connection within supply chains, with China only joining the WTO in December of that year. What’s more, the impact was lessened in 2001 by the relative infancy of consideration of working conditions as an element of quality.
This was less the case in 2008, and there was notable backsliding in both engagement and conditions. As one CSR executive recounted to me some time later, “We had made real progress and improvement in our factory base—and that was essentially lost in a matter of months based on a change in focus and new priorities.”
It can be argued that the focus and commitment around working conditions in the supply chain were not truly reinstated to pre-2008 levels until the tragic events of 2013/14 with the devastating loss of life in Bangladesh and Pakistan resulting from catastrophic fires and building failures.
Unlike 2008, the post-pandemic supply chain landscape will not look the same as it did a matter of weeks ago.
There will be a significant number of factories that will fail, with their workers and capabilities eliminated from the available sources of supply. For companies in market regions such as the U.S. and Europe, there is a logical expectation that there will be a focus on self-preservation, through actions like the cancellation of orders and delaying shipments and payments.
With that said, there is a real need to ensure that to the greatest extent possible, companies are taking into consideration the performance of factories and suppliers beyond simply price. Ultimately, some of the best partners in the supply chain have invested in critical elements to support the values of their partners be it fire safety, wages or environmental programs.
This is the time that there is a real need to appreciate those efforts, and understand that there is a choice in front of us. Do we look for a landscape where we have preserved and help save—whether through a small order or partial payment or receipt of product—those partners that have shared our values and are doing the right things or do we contribute to a landscape where the options are limited to producers who do not pay wages or operate in ways that are fundamentally unsafe or inhumane. The crisis will pass, and the key is whether we are looking for an environment that is a park with its creatures or a landfill with its creatures.
No doubt, times will be tough—and it is incumbent on all of us to think about how we can best shape the outcomes.
Randy Rankin is currently the Global Client Development Director in the Consumer Products Testing Assurance Services practice at Eurofins and has more than 25 years experience in the risk and supply chain management serving top-tier consumer products companies. During this period, Rankin has been involved in the development of industry standard methodologies for consideration of working conditions in the supply chain; and the development of company perspectives on supply chain risk management issues including social compliance.He can be approached at RandyRankin@eurofinsUS.com.